Traditional Crafting of Bells
The processing phases that lead to the birth of a bell require careful and patient work but above all experience and passion.
The first bells for liturgical use were made of wrought iron, were small and had an almost vertical profile, just slightly flared towards the bottom. In places where it was difficult to find iron ore or where it was very expensive, the bells were made of tin, similar in shape to those carried by cows.
In the 7th and 8th centuries, bells began to be cast in bronze, using an alloy containing four parts copper and one part tin. Traditionally gold and silver were also combined with the molten materials for devotional purposes.
The bell cast in bronze was originally very simple and rudimentary, without inscriptions, dates or embellishments, with an undefined shape.
The technique used for casting bells, initially practiced by monks/artisans, has evolved extraordinarily quickly. As early as the 9th century, bells were cast in nomadic workshops. Lay people soon became bell casters in addition to the monks, transporting their workshops from place to place. Between the ancient category of itinerant bell crafters and the modern category of established bell foundries lies that of semi-nomadic smiths, a practice more popular in previous centuries and up to the mid-1900s. These artisans, though owners of a permanent workshop and furnace, would set up temporary workshops in order to cast bells “on site” due to their large size or to avoid having to transport them to distant or inaccessible places. Even in the 1920s, the Marinelli foundry workers, moved craftsmen and equipment to Pompei for a few years to create the majestic peal of bells for the Marian Sanctuary, along with many other bronzes for the churches in the area.
The profession was passed down from father to son, forming a “corpus”, a group of specialists protective of their trade secrets which they kept with rigorous care as if a closed order. In Italy, from the 13th century onwards, foundrymen from Pisa, Lucca, Florence and Venice became particularly distinguished.
The Marinelli foundrymen were already establishing their business at the time, even if the first bell bearing the signature of Nicodemo Marinelli “anglonensis” the “historical” founder of the family, was found in the Frosinone area and dated 1339.
Today in the Marinelli foundry the techniques and materials used are the same as the ones used by the master craftsmen of the Middle Ages and the Renaissance. Technology has not accelerated the crafting process which can vary from two to many months. By the year 1700, the bell had finally taken on a well-defined shape, very similar to the shape it has today. However, the proportions between diameter and height had still not been perfected, therefore bells continued to maintain a tapered appearance. Subsequently, a bell scale was defined which indicated perfect proportions between thickness, weight, circumference and height, in relation to the desired tone. The bell can be considered a truncated cone inserted into a cube; its profile is drawn using a compass as there are no straight lines, as Diderot reports in the “Encyclopedie”, and this determines the note and quality of the bell.
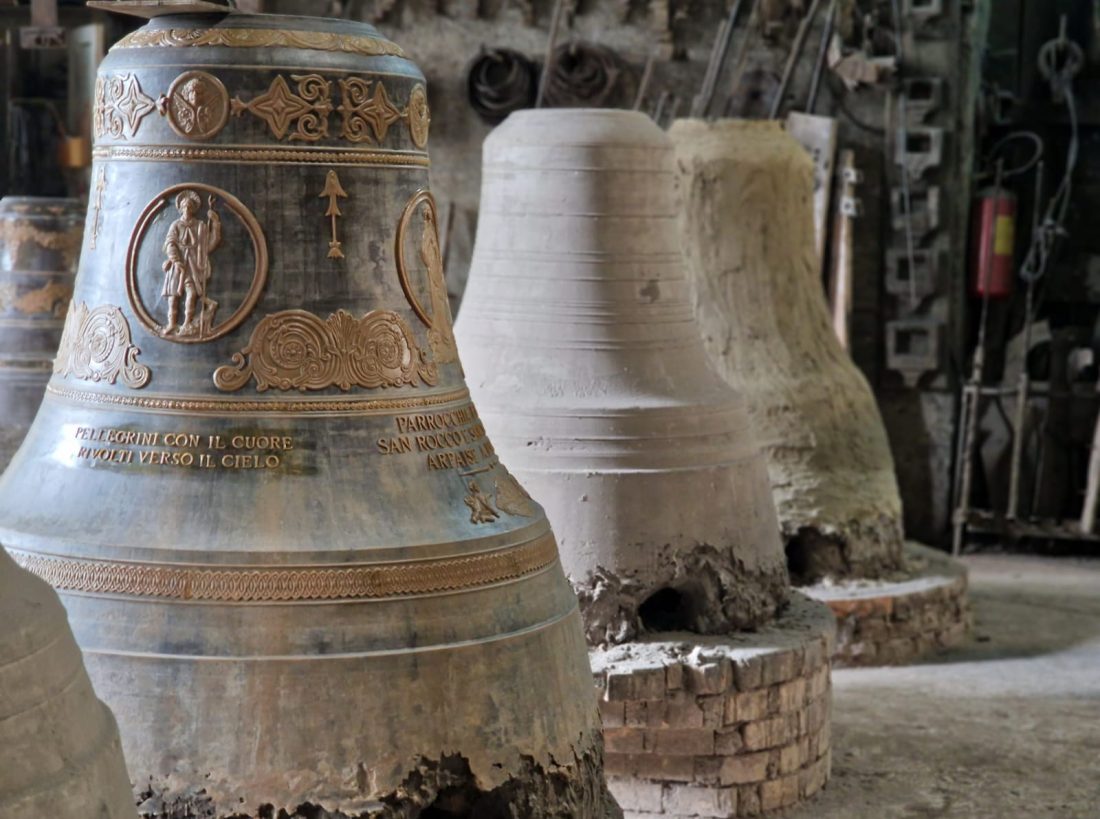
Processing steps in bell crafting
The bell core
Using a wooden template, a brick core is constructed, which is an exact model of the inside of the bell.
The false bell
The core is covered with layers of clay until a smooth profile is obtained, on which the molten wax shapes of the dedications, images and friezes are applied.
The Mantle
More clay is spread on top of the false bell to obtain the desired thickness.
Processing steps
Preparing the mold
We start by preparing a strickle board made of walnut wood that corresponds to the profile of the bell. This is used to build the CORE, a hollow brick structure that corresponds to the shape of the inside of the bell. Different layers of special clay are distributed over the core to obtain the FALSE BELL which is the exact model of the bell, having the same thickness as the bronze bell will have. On this perfectly smooth surface, molten wax friezes and inscriptions which dedicate and decorate the bell are applied.
The last molding phase consists in preparing the MANTLE, obtained by superimposing layers of clay. Once the mold is completed, the mantle is lifted to reveal the false bell which is then destroyed. The mantle is then repositioned over the core to create the cavity in which the bronze is poured.
At this point the mold is ready to be buried in the casting pit at the foot of the furnace, firmly clamped into place so that it remains still during casting. The bronze (78 parts copper and 22 parts tin) is melted in a large reverberatory furnace fueled by wood, at a temperature of around 1150° C.
Casting
The casting of a bell is the last step in a very long process. The birth of a new creature at the end of its gestation generates great apprehension and therefore requires blessings. At the opening of the furnace to begin the pour, “Santa Maria”, the Mother of all creatures, is invoked. This combination of mystical symbolism and collective emotion makes for an indescribably evocative event.
Final stages
After COOLING, the bell is extracted from the pit and moves on to the CLEANING phase where the core and mantle are removed and then the bell is cleaned and polished. The sound is tested with a tuning fork and, finally, a proportionate clapper and any required electronic systems for automatic tolling are applied. The bell is finally ready to be installed in a small chapel, in one of the most important bell towers in the world, on the desk of a famous person, or in the home of anyone who loves ART made by artisans.